Levitt-Safety Blog
content loaded
Page 1 of 11 — Total of 131 posts
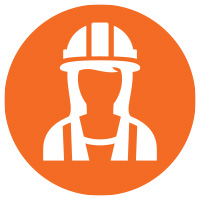
Sharon VincentJune 26, 2025
How to choose cut-resistant gloves
Over a third of workplace hand injuries involve cuts and often occur because workers are wearing the wrong hand protection—or worse, no hand protection! Unfortunately, the countless options on the market can make it difficult to ch...
Read More.png?width=1024&height=1019)
Victoria WebbApril 21, 2025
Sustainable Products for a Greener Future
Looking for ways to celebrate Earth Day? Consider switching to sustainable products that are not only eco-friendly but also contribute to a greener future. As more manufacturers invest in sustainable technology, the industrial safety spa...
Read More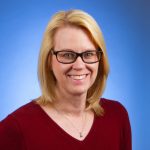
Leslie MolinApril 8, 2025
Choose the correct chemical suit with these 5 steps
Choosing an appropriate chemical suit for your job can seem like a daunting task. And, with hundreds of options available, it can be hard to know where to start. You might think suiting up in the highest level of protection is the surest...
Read More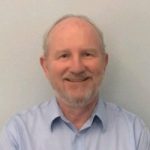
Gary RaeApril 4, 2025
ION Science explains Photo-Ionization Detectors in ‘What is a PID?’
This guest blog, contributed by our partners at ION Science, takes a deep dive into the technical aspects of photoionization detection (PID). While it's more technical than our usual content, it's packed with valuable information...
Read More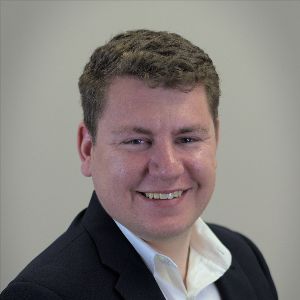
Zach Braun, CEO of SlateSafetyMarch 4, 2025
Rethinking Heat Stress for Modern Workforce
Each year heat related illnesses pose a serious threat to workers. Heat stress can escalate quickly, leaving workers vulnerable, supervisors unaware, and companies exposed to costly consequences. The is of particular concern for workers ...
Read More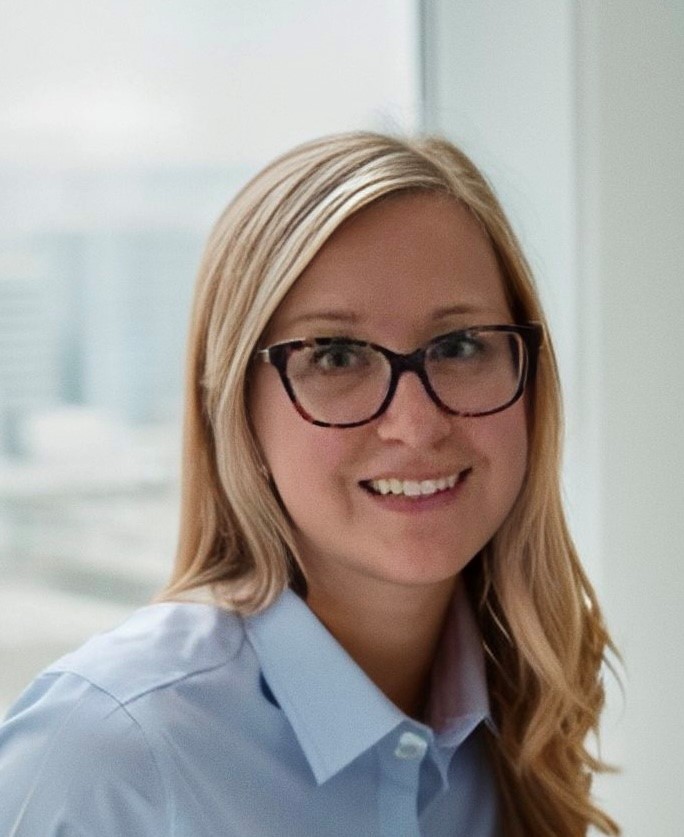
Nikki IslicFebruary 27, 2025
Innovative Applied Research to Support Safety and PPE design
The Canadian Institute for Safety, Wellness & Performance (CISWP) is based at Conestoga College and is the only work and health applied research centre in Canada's college system. It works to ensure that Canadian workplaces are s...
Read More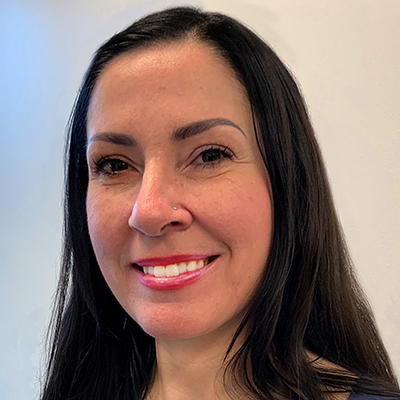
Renae CampbellJanuary 20, 2025
Meet Our Vehicle Fire Suppression Team – Shane Paul
Levitt-Safety prides itself on being an industry leader and expert in Vehicle Fire Suppression Systems (VFSS) . Located strategically across Canada, Levitt-Safety serves industries that include mining, agriculture, forestry, shipping and...
Read More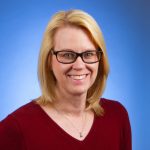
Leslie MolinJanuary 13, 2025
Addressing the Need for Women-Specific PPE: Ensuring Safety and Inclusivity
As a trusted Canadian health and safety distribution and service company, Levitt-Safety prioritizes the well-being and safety of all workers. In our previous blog PPE for Women: Real Solutions to keep all workers safe , we highlighted th...
Read More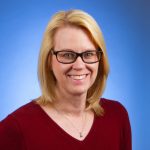
Leslie MolinJanuary 7, 2025
Get a grip this winter: How to walk on ice with confidence
Winter in Canada is great. You can play the best sports, the scenery is gorgeous and the world becomes your freezer. There's just one problem: Ice. Everywhere. Slip-and-fall accidents rank among the most common property accidents in ...
Read More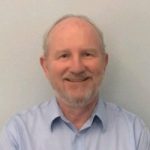
Gary RaeNovember 4, 2024
ChemDAQ Partners with Levitt-Safety to Provide PAA, H2O2, and EtO Gas Monitoring Solutions to Canada
[Press Release, Pittsburgh, PA, October 17, 2024] – ChemDAQ announced today that the company has entered into a distribution agreement with Levitt-Safety, a leading Canadian safety company, providing safety-related products, servic...
Read More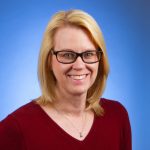
Leslie MolinSeptember 9, 2024
How to choose the best flashlight for your needs
Are you looking for info on picking the best flashlight? Then you've come to the right post! You'll learn about: what makes a flashlight bright the best battery option, and the highest performing light types.
Read More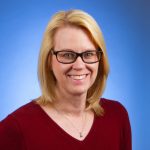
Leslie MolinSeptember 6, 2024
Find the best winter work gloves in Canada
This post is going to be your best friend this winter. We outline the best winter work gloves by category and explain what you need to look for when working outdoors in cold Canadian weather. Best winter work gloves by category: Best ove...
Read More